A numerical optimization process has been carried out in order to improve the performances of two helicoidal gears used to move the oil pump of a four cylinder diesel engine for a light commercial vehicle application. In particular the aim of this activity has been to reduce the noise generated by the gears under the normal operating conditions without penalizing their strength and reliability.
To do this modeFRONTIER has been used together with Helical3D which is a commercial software performing three-dimensional finite element analyses of gears taking into account the contact problem.
Among the several outputs deriving from a Helical3D analysis the most significative ones have been chosen as objectives of the optimization: the maximum bending stress at the tooth root of each gear, the maximum contact pressure and the peak to peak transmission error (PPTE). The first quantities are related to the gear reliability whereas the last one can be considered as a noise indicator. The optimization purpose has been to minimize the bending stresses, the contact pressure and the PPTE.
The input variables of the problem has been divided into two categories: the macro-geometrical variables and the micro-geometrical ones. The first category includes all the macroscopic quantities which are necessary for the definition of the gear dimensions and the tooth shape. To the second category belong all the microscopic modifications of the theoretical tooth profile.
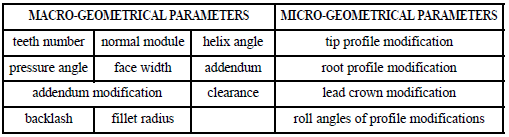
The whole optimization process has been conducted in two subsequent steps; in the first step only the macro-geometrical parameters has been taken into account while in the second step the micro-geometrical variables has been also added in the analysis.
An iterative procedure has been chosen to carry out each optimization step: at first a DOE is generated and a response surface created, then a virtual optimization is performed and a Pareto frontier is found; the designs belonging to the Pareto frontier are computed by Helical3D and the response surface is updated.
At the end of the optimization activity the predicted PPTE has been reduced of 70% without affecting the gear reliability. |